Self-cleaning screen featuring molded rubber strips that hold high-strength wires in place. Providing better screening action than traditional woven wire and greater open area than polyurethane, this screen media is designed to boost production by reducing costly, time-consuming blinding and pegging problems, while also delivering superior wear life. Diamond, Herringbone, and Straight wire slot openings for maximum output in a variety of dry or wet applications.
Self-cleaning screen made of woven wire cloth has an advantage of higher temperature resistance which polyurethane self-cleaning screen can not replace, it is typically used in sectors of road construction or asphalt mixing. The individual steel wires vibrate independently helping to avoid clogging or plugging while improving screen efficiency. This type of self-cleaning screen is generally applied in most common screening applications.
Woven wire screen having triangular openings features larger load bearing capacity, less deformation and higher screening accuracy in contrast to screens with diamond shaped openings.
Because some special materials have the tendency to adhere on the screen surface, or become wedge, due to their humidity,plasticity or shape. This was reduces the production capacity of the screen and increases the downtime of the machine considerably . To solve this problem we use this self-cleaning screens with crimped or straight wires, which vibrate independently from one another, being excited by the vibration of the machine and also by the weight of the material to be screened. This is a noticeable increase in production and a longer using life of the meshes. These meshes also offer a high percentage of screening surface, which makes them highly recommendable for improving the production capacity.
Besides, Polyurethane cross straps of the self-cleaning meshes was greater wear resistance than metal straps and increase the screen's wear life. The crippled wires obtain a precise and effective screening. The wires vibrate independently from another one, avoiding the material build-up, pegging and blinding.
It is particularly effective for screening crushed stone, sand and gravel, and materials with high water content, helping materials to stratification more quickly.
Compared to standard woven square mesh, the screening efficiency is improved by at least 30%.
Compared to standard woven wire screens with the same wire diameter, it has a larger effective wear area.
Effectively reduce or solve the problems of pegging or blinding.
It is particularly effective for screening crushed stone, sand and gravel, and materials with high water content, helping materials to stratification more quickly.
Compared to standard woven square mesh, the screening efficiency is improved by at least 30%.
Compared to standard woven wire screens with the same wire diameter, it has a larger effective wear area.
Effectively reduce or solve the problems of pegging or blinding.
Specifications
Opening sizes
2.0mm-45mm
Materials available
patented wire (65mn manganese steel wire), stainless steel, medium carbon steel, high carbon steel
Wire
>0.8mm
Screen size
Max. 3m width
Applications
- Sand and gravel industry
- Ore preparation plants
- Mining industry
- For wet, sticky, hard-to-screen materials
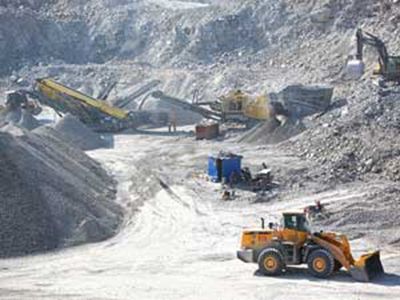
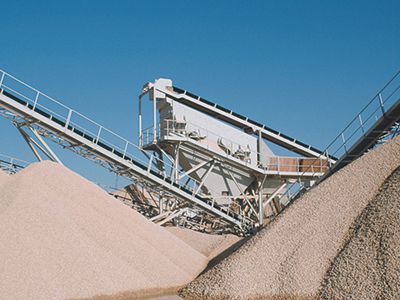
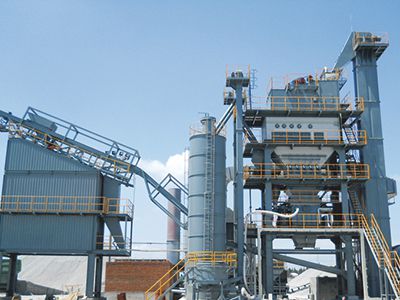
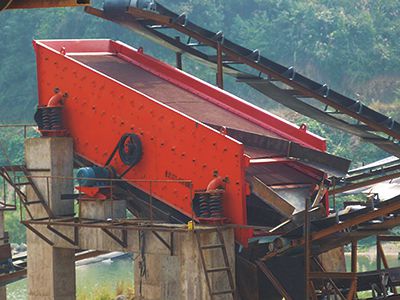
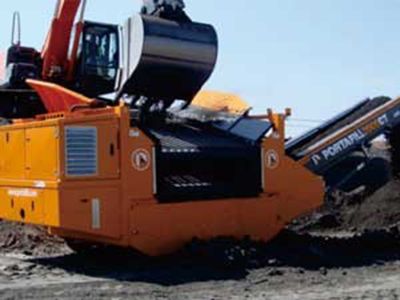
Gallery
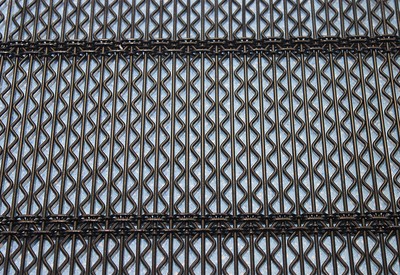
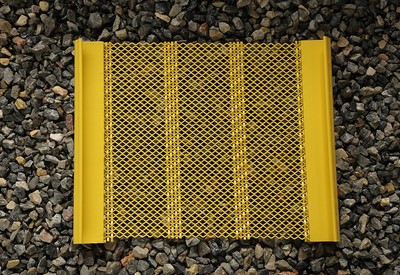
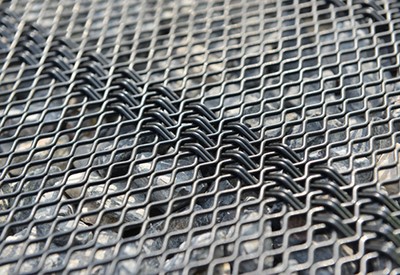
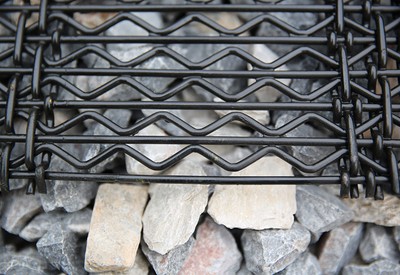