Polyurethane self-cleaning screen from Red Star can solve the clogging problems which frequently occur in conventional polyurethane screen panels. Our polyurethane screens are offered in various options of opening shape and installation method to be readily substituted for customer’s existing screens.
Polyurethane formulations can be adjusted to give hardness adapted to actual application needs, enabling the self-cleaning screen to achieve the right balance of flexibility, load bearing capacity and impact resistance.
Specifications
Material
Polyurethane
Opening size
>2mm
Thickness
>6mm
Screen size
Max.3m width
Polyurethane self-cleaning screen panels typically vary in specifications due to differences in manufacturers and product models. However, they generally include the following parameters:
Material specifications: Including the type of polyurethane material, density, hardness, and other related parameters.
Dimensions: Consisting of length, width, thickness, and possibly sieve hole size and shape.
Surface treatment: This may involve surface smoothing treatment, special protective layers, or coatings.
Self-cleaning efficacy: Evaluation indicators of self-cleaning performance, such as cleaning frequency and effectiveness.
Wear resistance: Typically assessed through parameters like tensile strength, hardness, etc., to evaluate its durability against wear.
Corrosion resistance: This parameter may include its resistance to different acidic or alkaline media.
Applicable temperature range: Some specifications may provide the temperature range within which the panel can be effectively used.
Installation method: This may involve details about installation hole positions, types, and other relevant information.
Other special requirements: Depending on specific application scenarios, there might be additional special requirements to consider.
Application
Polyurethane self-cleaning screen panels are suitable for various applications where efficient screening and prevention of blockages are required. Their primary applications include but are not limited to the following:
Mining and quarrying: Used in vibrating screens, screening machines, and other equipment to screen and classify raw materials such as ores, coal, and slag, preventing blockages caused by material adhesion.
Construction materials: Utilized in concrete production lines, asphalt mixing stations, and other equipment to screen aggregates such as sand and stone, ensuring the quality of construction materials.
Metallurgical industry: Employed in the screening of iron ore, copper ore, aluminum ore, and refining slag to extract and refine metallic minerals.
Chemical industry: Used in chemical production for processes such as solid-liquid separation, powder screening, screening of chemical raw materials, and classification of granular materials.
Food processing: Applied in the food industry to screen powdery materials such as flour, sugar, starch, and for the fine screening and grading of food raw materials.
Environmental engineering: Utilized in environmental projects such as wastewater treatment, solid waste treatment, for processes including solid-liquid separation, waste treatment, aiming to improve resource recovery efficiency and environmental protection.
Other industries: Also applicable in pharmaceuticals, cosmetics, papermaking, ceramics, and other industries to meet various screening, filtering, and separation requirements.
- Sand and gravel industry
- Ore preparation plants
- Mining industry
- For wet, sticky, hard-to-screen materials

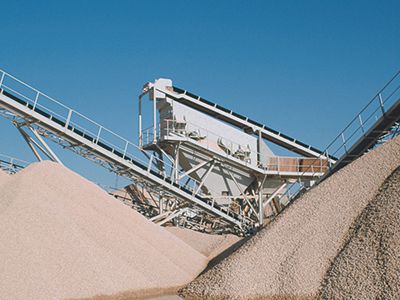
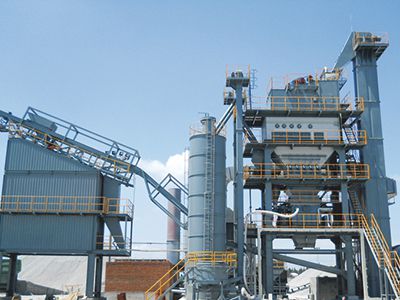
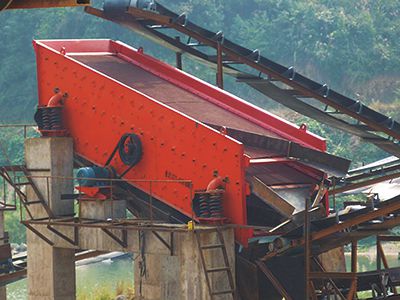
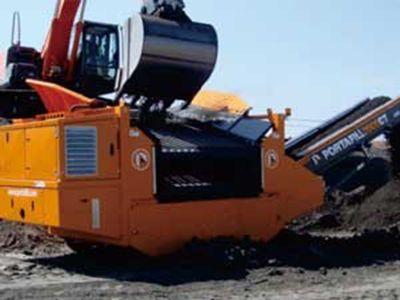